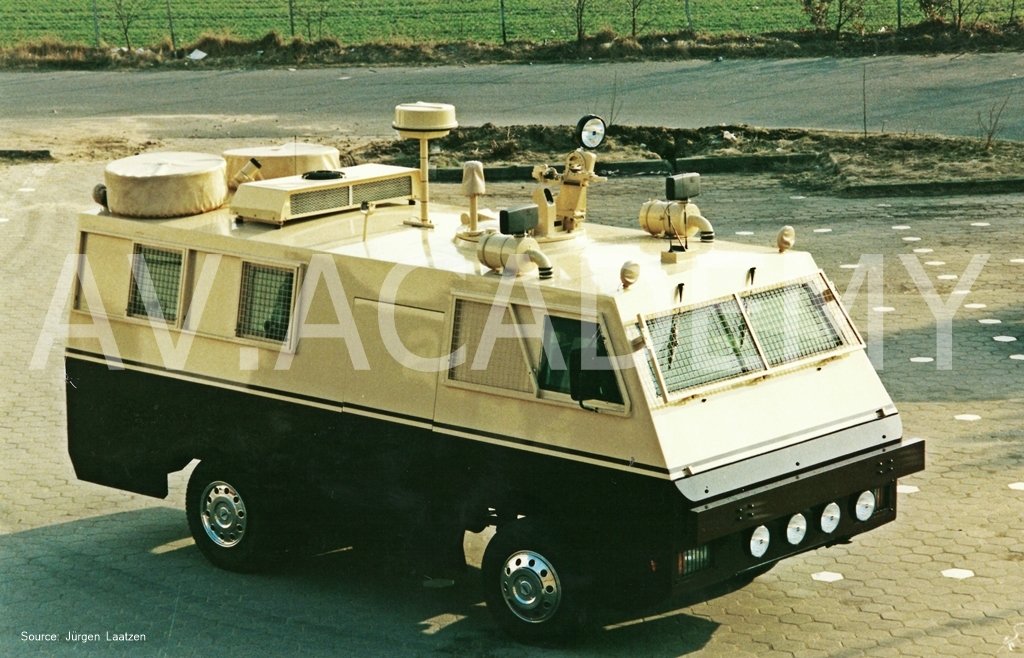
Back in the days, armoured vehicles appearance was - let's call it '80s style. Due to an easier production process, faster production times and the lack of any modern political correctness, armoured vehicles were allowed to look like a shoe-box on wheels, ready to tip over by the slightest attempt to drive a light bent.
Ballistic demands were lower, blast threats in many cases no issues, IEDs, VBIEDs or even EFPs only something the military was confronted with. But civil armoured vehicles, such as the famous Toyota Land Cruisers or the Mercedes S-Classes have ancestors that reach far back into the last century.
As always, the Germans brought it up - at least that is what they say...
One of the first professional armoured civil vehicles is claimed to be the "Big Benz" or "The Super Mercedes" Typ W 07. This iconic piece of steel, as well as its successors, got famous for transporting popes, businessmen and of course mass-murderers (not at once).
Even back in these days, the successor W150 was already equipped with 40mm armoured glass and 18mm of hardened steel. The engine fought its weight-battle together with two compressors that fired about 400hp to its back-wheels.
Today, 40mm of armoured glass is not very impressive anymore. Modern vehicles tested up to VPAM BRV 2009 VR10 easily double this thickness. But the 18mm steel plates of the old Mercedes fortress are still quite impressive. Self-carrying OEM vehicle structures with combinations of aluminium, cast-aluminium, carbon-fibre, high-strength and/or hot formed steel panels make it not easy on OEMs and retrofitters to integrate armour up to latest standards in combination with durability and blast integrity.
Especially low-cost productions have a hard time keeping up with these modern body designs as R&D costs are immense. Where the cheapest win the contracts, there is not much room for finite element analyses, live endurance or load testing, or even independent certifications via organizations like the Department Of Transport or the TÜV.
Cracking vehicle chassis is already a very common phenomenon, especially after a few years of hard operation in suspension unfriendly areas like war-zones or developing nations.
With modern materials for a frame- & body construction, these patterns of defects will increase if not deeply considered into the vehicle concept.
Armoured plating mounted directly to the OEM door-steel, without any supportive frames or interior support structures, give engineers plenty of headaches in times of plastic-tailgates (like installed on the latest Range Rovers).
And what does the customer want?
A Mercedes’ish / Audi’ish interior in top quality – like on the OEM vehicle.
To be fair, it is understandable.
The end-customer compares up-armoured vehicles with the OEM production line and of course the OEM armoured role-models of Mercedes, BMW and Audi. OEMs, in possession of all design patterns, measurements and data, have it easier to integrate complex safety cocoons into their existing chassis, adjust and reinforce active suspension parts, sensors, ABS / ESP programming and other weight relevant figures. Also, this trend will progress.
The combination of high-tech limousines and cheap armour solutions will have it much harder in the future, due to money eating Bits & Bites development.